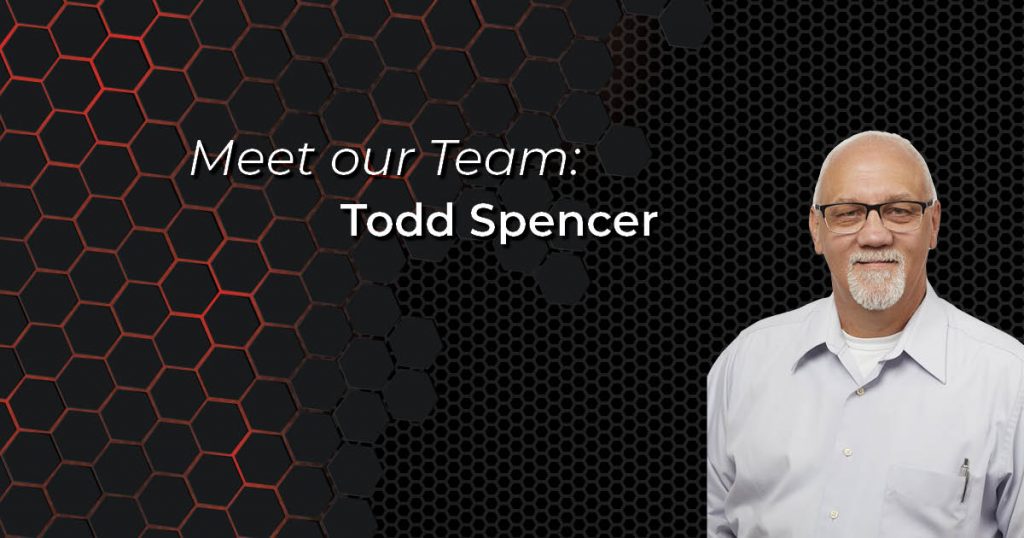
Meet Our Team: Todd Spencer
The Meet Our Team blog series gives you an inside look into our team members’ careers, exciting new projects, history with KFI, and a general
The Meet Our Team blog series gives you an inside look into our team members’ careers, exciting new projects, history with KFI, and a general
The Meet Our Team blog series gives you an inside look into our team members’ careers, exciting new projects, history with KFI, and a general
The Meet Our Team blog series gives you an inside look into our team members’ careers, exciting new projects, history with KFI, and a general
The Meet Our Team blog series gives you an inside look into our team members’ careers, exciting new projects, history with KFI, and a general
Join us to explore the ways that employees can grow their careers with KFI! Joining a new company as an entry-level employee with large career
Follow these steps to ensure you choose the right design partner for your project. Finding the right partner for your production project can feel daunting.
The Meet Our Team blog series gives you an inside look into our team members’ careers, exciting new projects, history with KFI, and a general
What to take into account when choosing the best plastics process for your next project. As the worlds leader in custom thermoformed solutions, Penda focuses
The Meet Our Team blog series gives you an inside look into our team members’ careers, exciting new projects, history with KFI, and a general
The Meet Our Team blog series gives you an inside look into our team members’ careers, exciting new projects, history with KFI, and a general